Introduction
Polymers form important components of our daily lives. Polymers are highly useful in domestic, industrial, and medical fields. The following are the reasons for the extensive use of polymers:
- Most polymers are non-toxic and safe to use.
- They have low densities (light in weight), so transporting polymers is easy.
- They possess good mechanical strength.
- They are resistant to corrosion and do not absorb moisture when exposed to the atmosphere.
- They function as good thermal and electrical insulators.
- They can be molded and fabricated easily.
- They possess aesthetic colors.
However, there are limitations to the use of polymers:
- Some polymers are combustible.
- The properties of polymers are time-dependent.
- Some cannot withstand high temperatures.
It is also interesting to note that many carbohydrates, proteins, enzymes, DNA, and RNA are natural polymers. Polymers can be defined as large molecules (macromolecules) formed by the linkage of small molecules called monomers. (In Greek, "poly" means many, and "mer" means units.)
E.g., polyethylene:
Thus, the repeated unit of a polymer is called a monomer. The number of repeating units in a polymer chain is called the degree of polymerization. For example, if 100 molecules of ethylene polymerize to give a polymer chain, the degree of polymerization is 100.
Important terms:
Homopolymer:
A polymer made up of only one type of monomer.
E.g., polyethylene: (-M-M-M-M-)n
Copolymer:
A polymer formed by the reaction between different monomers.
E.g., buna-S: (M₁-M₂-M₁-M₂)n
Tacticity:
The arrangement of functional groups on the carbon backbone of the polymer is called tacticity. It is mainly divided into three types:
-
Isotactic polymers: Polymers in which the functional groups are arranged on the same side.
E.g., PVC (Polyvinyl chloride): -
Atactic polymers: When there is no regular arrangement of functional groups on the backbone of the polymer chain, these polymers are called atactic polymers.
E.g., PVC (Polyvinyl chloride): -
Syndiotactic polymers: Polymers with an alternating arrangement of functional groups.
E.g., PVC (Polyvinyl chloride):
Classification of Polymers
View Image of classification here
Classification Based on Source or Origin
-
Natural Polymers: These polymers are found in nature, originating from plants, animals, or humans. Examples include:
- Proteins: Present in muscles, skin, and hair.
- Polysaccharides: Examples are cellulose in plants and starch.
- Nucleic Acids: Such as DNA and RNA.
- Natural Rubber: Latex derived from rubber trees.
-
Synthetic Polymers: These are man-made polymers created through industrial processes. Examples include:
- Plastics: Like polyethylene, PVC, and polystyrene.
- Synthetic Fibers: Such as nylon, polyester, and acrylic.
- Elastomers: Examples include neoprene, Buna-S, and Buna-N.
- Synthetic Rubbers: Such as SBR and EPDM.
-
Semi-Synthetic Polymers: Chemically modified natural polymers. Examples include:
- Cellulose Acetate: Used in photographic film.
- Rayon: A regenerated cellulose often used in textiles.
Classification Based on Structure
-
Linear Polymers: Composed of long, straight chains. These chains can pack closely, often making the polymer dense and strong.
- Examples: Polyethylene, PVC, and high-density polyethylene (HDPE).
-
Branched Polymers: Contain side chains attached to the main chain, which prevents tight packing and generally results in lower density and melting points.
- Examples: Low-density polyethylene (LDPE), amylopectin.
-
Cross-Linked Polymers: Have long chains interconnected by covalent bonds, creating a network structure that is usually hard, rigid, and brittle.
- Examples: Bakelite, vulcanized rubber, melamine.
-
Network Polymers: Highly cross-linked, forming a three-dimensional network. These are typically thermosetting plastics that do not melt when heated.
- Examples: Epoxy resin, phenol-formaldehyde resin.
Classification Based on Molecular Forces
-
Elastomers: Possess weak intermolecular forces, allowing them to stretch and return to their original shape, like rubber.
- Examples: Natural rubber, neoprene, Buna-S, Buna-N.
-
Fibers: Have strong intermolecular forces (e.g., hydrogen bonding), making them rigid and strong; fibers are often used in fabric production.
- Examples: Nylon, polyester, Kevlar.
-
Thermoplastics: These polymers have intermediate intermolecular forces. They soften when heated, allowing them to be reshaped, and are recyclable due to their ability to be remelted.
- Examples: Polyethylene, PVC, polystyrene, polypropylene.
-
Thermosetting Polymers: These are strongly cross-linked polymers that harden permanently upon heating and cannot be reshaped, making them non-recyclable.
- Examples: Bakelite, epoxy, melamine formaldehyde.
Classification Based on Polymerization Process
-
Addition Polymers: Formed by the repeated addition of monomers with double or triple bonds, without the release of any small molecules. This process is also called chain-growth polymerization.
- Examples: Polyethylene, polypropylene, polystyrene, PVC.
-
Condensation Polymers: Formed through a condensation reaction, releasing a small molecule (such as water, HCl, or methanol) in each step. This is also known as step-growth polymerization.
- Examples: Nylon (formed from hexamethylene diamine and adipic acid), polyester, Bakelite, urea-formaldehyde resin.
Classification Based on Response to Temperature
-
Thermoplastics: Soften upon heating and can be reshaped multiple times. They usually have linear or slightly branched structures, allowing chain mobility when heated.
- Examples: Polyethylene, polypropylene, polystyrene, PVC.
-
Thermosetting Polymers: These harden permanently when heated due to cross-link formation and cannot be reshaped.
- Examples: Bakelite, melamine, epoxy resins.
Classification Based on Biodegradability
-
Biodegradable Polymers: Can be decomposed by microorganisms into natural substances like water and carbon dioxide, reducing environmental impact.
- Examples: Poly(lactic acid) (PLA), polyhydroxyalkanoates (PHA), polycaprolactone (PCL), starch-based polymers.
-
Non-Biodegradable Polymers: Resistant to microbial breakdown, these polymers may persist in the environment for centuries, posing ecological challenges.
- Examples: Polyethylene, polypropylene, PVC, polystyrene.
Classification Based on Functionality of Monomers
-
Homopolymers: Consist of only one type of monomer, resulting in identical repeating units.
- Examples: Polyethylene (from ethylene monomers), polyvinyl chloride (from vinyl chloride monomers).
-
Copolymers: Composed of two or more different types of monomers. Copolymers can be classified based on the arrangement of monomers:
- Random Copolymer: Monomers are arranged randomly along the chain. Example: Styrene-butadiene rubber (SBR).
- Alternating Copolymer: Monomers alternate in a regular pattern. Example: Nylon-6,6.
- Block Copolymer: Blocks of one type of monomer alternate with blocks of another. Example: Polyurethane.
- Graft Copolymer: Chains of one monomer are grafted onto the backbone of another type. Example: Grafted polyethylene.
Glass Transition Temperature
The glass transition temperature () is a critical point for polymers and other amorphous materials (such as glass and some ceramics). Below this temperature, the material transitions from a rubbery, flexible, or viscous state to a hard, brittle, glass-like state. It marks the temperature at which the amorphous regions of a polymer become rigid due to the freezing of molecular motion, particularly the movement of polymer chains.
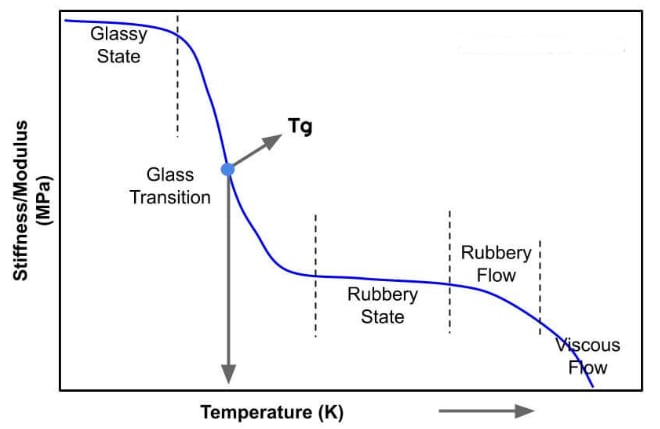
-
Not a Phase Transition: Unlike melting, the glass transition is not a true thermodynamic phase transition (e.g., from solid to liquid). Instead, it is a gradual transition that occurs over a range of temperatures, without the involvement of latent heat.
-
Amorphous Materials: The glass transition occurs in the amorphous (disordered) regions of a polymer. In semi-crystalline polymers (like polyethylene and polypropylene), applies only to the amorphous parts, while the crystalline regions melt at a higher temperature known as the melting temperature ().
-
Influence on Mechanical Properties: Below , materials are hard, brittle, and glass-like. Above , they become rubbery, flexible, and exhibit viscoelastic properties. For example:
- Below : The polymer is rigid and may shatter upon impact.
- Above : The polymer becomes flexible and can withstand stretching or bending.
-
Dependence on Chain Mobility: The glass transition occurs because molecular motion in the polymer chains becomes restricted below . As the temperature decreases, the chains lose flexibility, and molecular mobility decreases until the material reaches a glassy state.
Factors Affecting
-
Chemical Structure: The chemical composition of the polymer significantly influences . For instance:
- Rigid groups in the polymer backbone (e.g., benzene rings in polystyrene) increase due to restricted rotation.
- Flexible groups or long side chains (as in polyethylene) lower by allowing greater chain mobility.
-
Intermolecular Forces: Stronger intermolecular forces (e.g., hydrogen bonding) lead to an increased because they restrict molecular motion. Polymers such as polyvinyl alcohol, which exhibit strong hydrogen bonding, have a higher .
-
Molecular Weight: Generally, higher molecular weights result in a higher because longer chains become more entangled and less mobile.
-
Cross-Linking: Cross-linked polymers (e.g., vulcanized rubber) exhibit a higher due to restricted chain mobility, as the cross-links limit the movement of chains relative to each other.
-
Plasticizers: The addition of plasticizers (small molecules that disrupt intermolecular forces) lowers by increasing the free volume between polymer chains, facilitating easier movement. This is why plasticizers are often used to enhance the flexibility of materials like PVC at lower temperatures.
Significance of
-
Determines Material Properties:
- Below : The polymer behaves as a brittle, glass-like material. It is hard and stiff, with a tendency to shatter under stress.
- Above : The polymer becomes rubbery, flexible, and exhibits viscoelastic properties. This shift is crucial for applications that rely on elasticity, such as elastomers.
-
Temperature Range for Applications: Understanding is essential for selecting polymers suited to specific temperature conditions. For example, a polymer with a high is preferable for applications requiring rigidity at room temperature (e.g., polystyrene in plastic cutlery), while a low polymer, like polyethylene, is ideal for applications that demand flexibility.
-
Effect on Mechanical and Electrical Properties: Mechanical properties (such as hardness, toughness, and tensile strength) and electrical properties (like insulation resistance) are directly influenced by . For instance, the insulation properties of a polymer may decline above as it becomes more flexible and conductive.
-
Design of Polymer Blends and Copolymers: can be manipulated through copolymerization and blending, allowing for the customization of polymers for specific applications. By combining polymers with different values, manufacturers can produce materials with an optimal balance of rigidity and flexibility.
-
Thermal Stability and Processing Conditions: During processing, serves as a critical parameter, indicating the temperature at which the polymer becomes pliable. For molding, extrusion, and other manufacturing processes, heating the polymer slightly above facilitates shaping.
-
Relevance in Product Life and Performance: impacts the durability of polymers under varying environmental conditions. Polymers exposed to temperatures above their may experience a loss of mechanical strength over time, affecting product performance and longevity. For example, packaging materials are designed with considerations to prevent deformation during transport.
Synthesis of
The glass transition temperature () itself is not synthesized; rather, it is a property that emerges from the polymer’s structure and the conditions under which it is synthesized. However, the synthesis of polymers can be controlled to adjust or optimize depending on the intended application.
-
Monomer Selection:
- Rigid Monomers: Polymers made from rigid monomers, such as aromatic compounds (e.g., styrene, which contains a benzene ring), tend to have higher values due to restricted chain mobility.
- Flexible Monomers: Monomers with more flexible structures (e.g., ethylene) contribute to a lower , allowing for greater chain movement at lower temperatures.
-
Chain Length and Molecular Weight:
Higher molecular weights generally result in polymers with increased chain entanglement, which raises by limiting chain mobility. The polymerization process can be controlled to achieve the desired molecular weight, thus influencing .
-
Copolymerization:
- Random or Block Copolymers: By copolymerizing two or more monomers with different properties (e.g., one with a high and one with a low ), the resulting copolymer’s can be finely tuned. For example, incorporating a soft, flexible monomer into a rigid polymer can reduce , enhancing flexibility.
- Alternating and Gradient Copolymers: Different arrangements of monomers in copolymers can also affect . Gradient copolymers gradually change from one type of monomer to another, providing a smoother transition in properties, including .
-
Cross-Linking:
Cross-linking involves creating covalent bonds between polymer chains, forming a network structure that increases rigidity and raises . The density of cross-linking can be controlled during synthesis (e.g., through vulcanization in rubber), allowing for precise adjustments of .
-
Incorporation of Plasticizers:
During or after synthesis, plasticizers (small, flexible molecules) can be added to lower by increasing the free volume within the polymer. This technique is commonly used in PVC manufacturing to enhance flexibility for applications like cables and flexible tubing.
-
Degree of Crystallinity:
The crystallinity of polymers creates rigid regions, which raises the of the amorphous regions. Semi-crystalline polymers (e.g., PET, polyethylene terephthalate) are synthesized with specific processing techniques to control crystallinity, thereby influencing .
-
Functional Groups and Chemical Modifications:
Certain functional groups, such as polar groups (e.g., -OH, -COOH), can increase intermolecular interactions like hydrogen bonding, which raises . Chemical modification techniques, such as introducing polar groups or grafting different side chains, can be employed post-synthesis to adjust .
Properties and Applications of Polypropylene (PP)
Polypropylene (PP) is a thermoplastic polymer derived from the monomer propylene. It is one of the most widely produced plastics globally, known for its versatility, durability, and cost-effectiveness.
Properties of Polypropylene (PP)
-
Mechanical Properties:
- High Strength-to-Weight Ratio: PP is lightweight yet strong, making it suitable for applications requiring both durability and low weight.
- Good Impact Resistance: PP can absorb significant energy upon impact, although it may become brittle at very low temperatures.
- Flexibility and Toughness: It offers good flexibility, especially in copolymer forms, and can withstand repeated stress.
-
Thermal Properties:
- High Melting Point: PP has a melting point of approximately 160°C, making it suitable for heat-related applications.
- Low Thermal Conductivity: It serves as an effective thermal insulator, beneficial in applications where heat retention is necessary.
- Moderate Heat Resistance: While it has a high melting point, prolonged exposure to high temperatures can degrade PP.
-
Chemical Resistance:
- Resistant to Chemicals and Solvents: PP is resistant to many acids, bases, and organic solvents, making it ideal for chemical storage and packaging.
- Low Water Absorption: PP has low moisture absorption, helping to maintain its properties in wet environments.
-
Electrical Properties:
- Excellent Insulation: PP is a good electrical insulator, making it suitable for electrical and electronic applications.
- Low Dielectric Constant and Loss Factor: These properties allow it to be used in various insulation and electronic applications.
-
Aesthetic Properties:
- Good Surface Finish: PP can be molded into complex shapes with a smooth finish, often used in applications requiring a clean and attractive appearance.
- Easy to Dye and Color: It can be readily colored or dyed, allowing for custom designs.
-
Environmental Properties:
- Recyclable: PP is easily recyclable, making it environmentally friendly and suitable for sustainable applications.
- Resistant to Environmental Stress Cracking: PP maintains its integrity even under various environmental stresses.
Applications of Polypropylene (PP)
Given its diverse properties, polypropylene (PP) is utilized across many industries:
-
Packaging Industry:
- Food Containers: PP is widely used for food containers, lunch boxes, and yogurt cups due to its non-toxic, food-safe characteristics and excellent heat resistance.
- Bottle Caps and Lids: Its flexibility and impact resistance make it suitable for caps, lids, and closures.
- Flexible Packaging Films: PP is commonly used for packaging films, bags, and laminates because of its transparency and flexibility.
-
Automotive Industry:
- Bumpers and Interior Components: PP is often used in car bumpers, dashboard components, and interior trims due to its durability and lightweight nature.
- Battery Cases and Covers: Its chemical resistance and electrical insulation properties make it suitable for battery enclosures.
-
Textile Industry:
- Carpets and Rugs: PP fibers are used in carpets, rugs, and mats due to their stain resistance and durability.
- Non-Woven Fabrics: PP is used in disposable diapers, medical gowns, and masks because of its low cost and ease of production.
-
Medical Industry:
- Syringes and Medical Containers: The chemical resistance and sterility of PP make it ideal for syringes, test tubes, and other medical containers.
- Implants and Medical Devices: Its biocompatibility makes it suitable for certain implantable medical devices.
-
Household and Consumer Goods:
- Furniture and Storage: PP is used in household furniture, storage containers, and organizers due to its durability and cost-effectiveness.
- Appliances: Its heat resistance and electrical insulation properties make it suitable for components in household appliances.
-
Electrical and Electronics Industry:
- Insulation for Wires and Cables: PP's excellent insulation properties make it useful for wiring and cable insulation.
- Capacitor Films: Due to its low dielectric constant, PP is utilized in capacitor films and other electronic components.
-
Industrial Applications:
- Chemical Tanks and Pipes: The corrosion and chemical resistance of PP make it ideal for chemical storage tanks and piping systems.
- Laboratory Equipment: It is commonly used for beakers, petri dishes, and other lab equipment due to its chemical inertness.
-
Agriculture:
- Greenhouse Covers: PP is employed in greenhouse covers and agricultural films due to its transparency and UV resistance when stabilized.
- Irrigation Systems: Pipes and fittings made from PP are widely used in irrigation systems because of their durability and resistance to chemicals.
PVC
Polyvinyl Chloride (PVC): The monomer used for the manufacture of PVC is vinyl chloride. PVC is the third most produced plastic in the world, after polyethylene and polypropylene, known for its versatility, durability, and resistance to environmental degradation. Vinyl chloride is prepared by treating acetylene with HCl at 60-80°C in the presence of a metal oxide catalyst:
Polyvinyl chloride is produced by heating vinyl chloride in the presence of benzoyl peroxide or :
Properties of PVC:
- Durability: PVC is highly durable and resistant to environmental stressors, making it suitable for long-term use.
- Chemical Resistance: It resists acids, bases, salts, and alcohols, although it can be affected by certain solvents and organic compounds.
- Rigidity and Flexibility: PVC can be manufactured in both rigid and flexible forms, depending on the additives used.
- Flame Resistance: PVC is inherently flame-retardant due to its high chlorine content.
- Electrical Insulation: It possesses good insulating properties, making it suitable for cables and wiring.
There are two kinds of PVC plastics:
-
Rigid PVC (Unplasticized PVC): This form of PVC is a chemically inert and non-flammable powder with a high softening point of 148°C. It is used for making safety helmets, refrigerator components, and mudguards for bicycles and motorcycles.
-
Plasticized PVC: This type is produced by mixing plasticizers, such as dibutyl phthalate, with PVC resin. It is used for making raincoats, tablecloths, handbags, curtains, electrical insulators, and components for radios and televisions, as well as beachwear shoes.
PMMA
Polymethyl methacrylate (PMMA) is a versatile thermoplastic polymer widely used across various industries due to its favorable properties.
Chemical Structure and Properties
-
Chemical Formula: The chemical structure of PMMA is based on the polymerization of methyl methacrylate monomers, with the general formula (C_5H_8O_2).
-
Physical Properties:
- Appearance: Clear, transparent material.
- Density: Approximately 1.18 g/cm³.
- Thermal Stability: PMMA has a glass transition temperature ((T_g)) of about 100°C (212°F).
- Softening Point: PMMA does not have a defined melting point but begins to soften at around 160-170°C (320-338°F).
- UV Resistance: PMMA exhibits good UV stability, making it suitable for outdoor applications.
- Scratch Resistance: PMMA is more prone to scratching compared to glass but can be treated with coatings to enhance its durability.
Production Methods
PMMA is produced through various polymerization methods, including:
- Bulk Polymerization: Monomers are polymerized in bulk, producing solid PMMA.
- Suspension Polymerization: Monomers are dispersed in a liquid medium, allowing for controlled particle size.
- Emulsion Polymerization: Involves the polymerization of monomers in an aqueous environment, resulting in a latex that can be used in coatings and adhesives.
Applications
PMMA's unique properties make it suitable for a wide range of applications:
- Optical Applications: Used in lenses for glasses, camera lenses, and optical fibers due to its high clarity and light transmittance.
- Signage and Displays: Commonly used in illuminated signs, displays, and showcases.
- Aerospace and Automotive: Utilized for transparent components such as canopies, windows, and light covers due to its lightweight and shatter-resistant characteristics.
- Medical Devices: Employed in applications such as intraocular lenses, dental prosthetics, and surgical instruments because it is biocompatible.
- Home and Office: Used in products like aquariums, skylights, and protective barriers.
Advantages
- Clarity: High optical clarity, comparable to glass.
- Lightweight: Much lighter than glass, making it easier to handle and transport.
- Impact Resistance: More resistant to shattering than glass.
- Versatility: Can be easily molded and fabricated into complex shapes.
Disadvantages
- Scratch Sensitivity: More prone to scratching than glass.
- Chemical Resistance: Not as resistant to certain chemicals, solvents, and high temperatures.
- Brittleness: Can become brittle over time, especially when exposed to UV light.
Polyurethanes
Polyurethanes are a diverse group of polymers composed of organic units joined by urethane (carbamate) links. They are known for their versatility and are used in a wide range of applications.
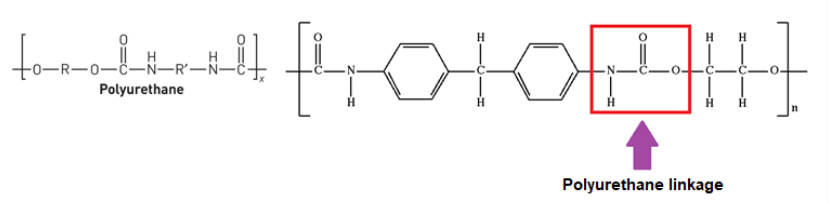
Chemical Structure
- Chemical Composition: Polyurethanes are formed by the reaction of a polyol (an alcohol with multiple hydroxyl groups) and a diisocyanate (a compound with two isocyanate groups). The reaction results in the formation of a urethane linkage (-NH-CO-O-).
- Structure: The structure can vary widely based on the choice of polyols and isocyanates, leading to different physical properties and applications.
Properties
- Flexibility and Elasticity: Polyurethanes can be produced in various forms, from soft and flexible to rigid and tough, depending on their formulation.
- Durability: They exhibit excellent wear resistance, making them suitable for high-stress applications.
- Chemical Resistance: Generally resistant to oils, solvents, and chemicals, although specific resistance depends on the formulation.
- Thermal Stability: Polyurethanes have good thermal stability and can withstand a range of temperatures, though specific grades may have limits.
- Lightweight: Many polyurethane products are lightweight, making them ideal for applications where weight is a concern.
Types of Polyurethanes
Polyurethanes can be categorized based on their physical form and properties:
- Flexible Polyurethanes: Used in cushioning, automotive interiors, and flexible foam applications. They are soft and resilient.
- Rigid Polyurethanes: Commonly used in insulation materials, construction, and structural components due to their strength and thermal insulation properties.
- Elastomeric Polyurethanes: These have rubber-like properties and are used in applications requiring high elasticity, such as seals, gaskets, and wheels.
- Coatings and Adhesives: Polyurethanes can be formulated as paints, varnishes, and adhesives, providing protective and aesthetic finishes.
- Thermoplastic Polyurethanes (TPU): These can be processed like thermoplastics and are used in applications requiring flexibility and durability, such as shoe soles and medical devices.
Epoxy Resins
Epoxy resins are a class of reactive polymers and prepolymers that are widely utilized in various applications due to their excellent mechanical properties, chemical resistance, and adhesive qualities.
Chemical Structure:
-
Basic Composition: Epoxy resins are formed from the reaction of epichlorohydrin and bisphenol A (or other polyols) through a process called polymerization. The key functional group in epoxy resins is the epoxide group (-O-).
-
Curing Process: Epoxy resins require a curing agent (hardener) to initiate cross-linking, resulting in a thermosetting polymer. The choice of hardener can significantly influence the properties of the final product.
Properties:
- Adhesive Strength: Epoxy resins exhibit excellent adhesion to a variety of substrates, including metals, glass, wood, and plastics.
- Mechanical Strength: They possess high tensile strength, impact resistance, and stiffness, making them suitable for structural applications.
- Chemical Resistance: Epoxy resins are resistant to many chemicals, including solvents, oils, and acids, making them ideal for protective coatings and linings.
- Thermal Stability: Epoxy resins can withstand a wide range of temperatures, although their thermal resistance depends on the specific formulation.
- Electrical Insulation: They have excellent electrical insulating properties, making them suitable for electrical and electronic applications.
Types of Epoxy Resins:
- Liquid Epoxy Resins: Commonly used in coatings, adhesives, and composites, these resins are usually low-viscosity and can be easily applied.
- Solid Epoxy Resins: Typically used in applications requiring high mechanical strength and heat resistance, such as in the aerospace and automotive industries.
- Modified Epoxy Resins: Altered with additives or co-monomers to enhance specific properties like flexibility, toughness, or chemical resistance.
- Thermal-Curable Epoxy Resins: Used in high-performance applications, these resins cure at elevated temperatures, providing superior thermal and mechanical properties.
- Ambient-Cure Epoxy Resins: These cure at room temperature and are commonly used in construction, adhesives, and coatings.
Applications: Epoxy resins are utilized across various industries, including:
- Adhesives: Widely used as strong bonding agents in construction, automotive, and manufacturing.
- Coatings: Applied as protective coatings for metal, concrete, and wood surfaces due to their durability and chemical resistance.
- Composites: Used as matrix materials in fiber-reinforced composites for aerospace, automotive, and sports equipment.
- Electrical and Electronic Components: Employed as insulators and encapsulants in electronic devices due to their excellent electrical properties.
- Construction: Used in flooring systems, repair materials, and as grouts and sealants.
- Marine Applications: Used for boat building and repair, providing resistance to moisture and chemicals.
Silicone Rubber
Silicone rubber is a durable and highly resistant elastomer (rubber-like material) composed of silicone (a polymer) that contains silicon along with other molecules. Known for its excellent thermal stability, water resistance, and biocompatibility, silicone rubber is widely used in industries ranging from medical devices to automotive parts.
Its structure consists of:
- A siloxane backbone (a silicon-oxygen chain).
- An organic moiety bound to the silicon.
The unique features of silicone rubber originate from its molecular structure, which contains both inorganic and organic groups.
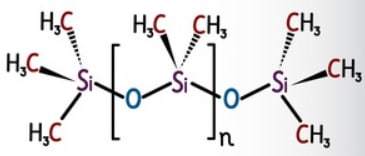
Properties:
- Thermal Stability: It can withstand extreme temperatures, typically from -55°C to +300°C (-67°F to +572°F), without significant degradation.
- Flexibility and Elasticity: Silicone rubber is highly flexible and retains its elasticity even at low temperatures.
- Chemical Resistance: It is resistant to water, ozone, UV light, and many chemicals, making it suitable for both indoor and outdoor applications.
- Electrical Insulation: Silicone rubber is an excellent electrical insulator, making it ideal for applications in electronics and electrical components.
- Biocompatibility: Silicone rubber is non-toxic and hypoallergenic, making it suitable for medical devices and implants.
- Water Resistance: It is inherently hydrophobic (water-repellent) and resistant to mold and mildew.
Types of Silicone Rubber:
- Room-Temperature Vulcanizing (RTV) Silicone: Cures at room temperature and is used in adhesives, sealants, and coatings; often employed in household and industrial applications.
- High-Temperature Vulcanizing (HTV) Silicone: Requires high temperatures to cure and is often used for molded parts and components that need high heat resistance.
- Liquid Silicone Rubber (LSR): A two-part silicone that is injected into molds to produce parts with high precision and flexibility; commonly used in medical, automotive, and consumer goods.
- Fluorosilicone Rubber: Combines the properties of silicone with enhanced chemical resistance, especially to fuels and solvents, making it ideal for aerospace and automotive applications.
- Foamed Silicone Rubber: Contains air or gas bubbles to create a spongy, flexible material used for gaskets, insulation, and cushioning applications.
Applications: Silicone rubber's versatility and durability make it valuable across various industries:
- Medical and Healthcare: Used in implants, tubing, catheters, and wound dressings due to its biocompatibility and flexibility.
- Automotive and Aerospace: Employed in gaskets, seals, hoses, and O-rings, as it withstands extreme temperatures and chemical exposure.
- Electronics and Electrical: Used in connectors, insulators, and cable jacketing for its electrical insulation and thermal stability.
- Construction: Applied as sealants, adhesives, and coatings in construction materials for its water resistance and flexibility.
- Household and Consumer Products: Found in kitchenware, baby products, and wearable devices due to its non-toxic nature and heat resistance.
- Food Industry: Used in baking molds, spatulas, and other utensils, as it is food-safe and resistant to high temperatures.
PET
Polyethylene terephthalate (PET) is a versatile thermoplastic polymer belonging to the polyester family. PET is commonly used in fibers, packaging, and molded parts and is known for its excellent strength, transparency, and recyclability.
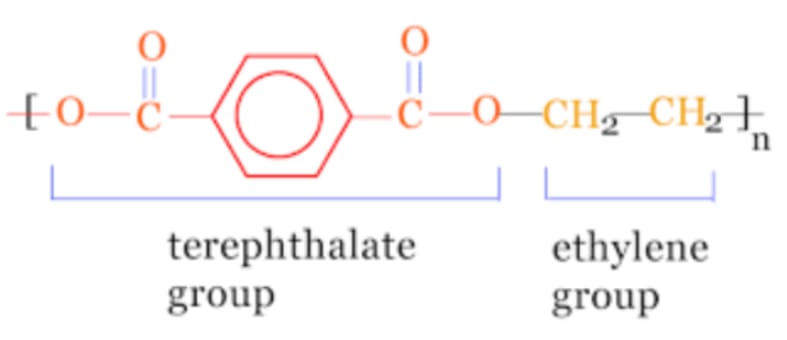
Chemical Structure:
- Polymer Composition: PET is made by the polymerization of ethylene glycol and terephthalic acid or dimethyl terephthalate. Its chemical structure includes repeating ester groups, which provide strength and durability.
- Crystalline and Amorphous States: PET can exist in both crystalline and amorphous forms, which influence its clarity and rigidity. Crystalline PET is opaque and more rigid, while amorphous PET is transparent and flexible.
Properties:
- Crystal Clear Polymer: PET is a crystal clear polymer with good purity. The sparkling PET bottles are a common sight and attract attention due to their brilliant clarity.
- Purity: PET products comply with international food contact regulations and maintain good taste.
- Safety: Objects made from PET, such as bottles, are tough and virtually unbreakable, making them suitable for storage and transportation. This polymer has high impact and tensile strength, making it ideal for carbonated products.
- Good Barrier: PET products have low permeability to oxygen, carbon dioxide, and water, helping to maintain the integrity of products and ensuring good shelf life.
- Lightweight: The lightweight nature of PET products reduces shipping costs compared to glass products.
- No Leakage or Damage: The absence of a weld line in the base of PET bottles prevents leakage and damage.
- Recyclable: PET is recyclable and can be reshaped into various forms.
- Good Resistance Power: PET products exhibit good resistance to various chemicals, including acids and bases.
Types of PET:
- PET Film: Often referred to as Mylar, PET film is used for packaging and in electronics, solar panels, and insulation.
- PET Fibers: Used in textiles, carpets, and industrial applications; commonly found in polyester fabrics.
- Amorphous PET (APET): Transparent and used in packaging where visibility and aesthetics are important.
- Crystalline PET (CPET): More opaque and has higher heat resistance, often used in microwaveable trays and food containers.
- Recycled PET (rPET): Processed from post-consumer PET products like bottles, often used in textiles, packaging, and automotive parts.
Applications:
PET's unique combination of properties makes it ideal for a variety of industries and applications:
- Beverage Bottles: PET is widely used for water, soft drink, and juice bottles due to its clarity, strength, and low weight.
- Food Packaging: PET trays, containers, and films are common in food packaging because of their gas barrier properties.
- Textiles and Fibers: PET is spun into polyester fibers used in clothing, upholstery, and industrial fabrics.
- Electronics: Used in insulation materials and as a substrate in electronic components due to its thermal and dielectric properties.
- Automotive: Used in belts, hoses, and other components requiring strength and thermal stability.
- Medical: Utilized for medical packaging and in certain medical devices.
Lexan
Lexan is a brand name for a type of polycarbonate (PC) resin produced by SABIC. It is renowned for its exceptional impact resistance, optical clarity, and thermal stability. Lexan is widely used in applications that require a tough, transparent material, such as bulletproof glass, safety goggles, and automotive parts.
Chemical Structure:
- Polycarbonate Base: Lexan is derived from polycarbonate, a thermoplastic polymer characterized by repeating carbonate groups (-O-(C=O)-O-) in its backbone. This structure contributes to Lexan’s toughness and high-temperature resistance.
- Molecular Structure: The molecular architecture of polycarbonate imparts strength and impact resistance while keeping the material relatively lightweight and transparent.
Properties:
- High Impact Resistance: Lexan is virtually unbreakable, with impact resistance up to 250 times greater than glass and approximately 30 times greater than acrylic.
- Optical Clarity: Lexan is highly transparent, offering optical clarity that makes it ideal for applications requiring clear materials, such as windows and eyewear.
- Thermal Stability: Lexan retains its properties across a wide temperature range, typically from -40°C to 120°C (-40°F to 248°F).
- Lightweight: Despite its strength, Lexan is much lighter than glass, facilitating easier handling and transport.
- UV Resistance: While standard Lexan can yellow over time due to UV exposure, UV-stabilized grades are available for outdoor applications.
- Moldability: Lexan can be molded into complex shapes, making it suitable for a variety of applications requiring design flexibility.
- Chemical Resistance: Lexan is resistant to many chemicals, although it can be susceptible to certain solvents and abrasive cleaners.
Applications:
Lexan's unique combination of strength, clarity, and versatility makes it suitable for numerous industries and applications:
- Safety and Security: Used in bullet-resistant glass (commonly referred to as bulletproof glass) for banks, police stations, and secure facilities, as well as in riot shields and other protective gear for law enforcement.
- Automotive and Aerospace: Employed for headlights, windows, and sunroofs due to its impact resistance and thermal stability.
- Construction and Architecture: Utilized in windows, skylights, and roofing materials that require both transparency and strength; also used for protective barriers in public spaces and offices.
- Electronics: Found in housings for mobile phones, laptops, and other electronic devices. Although less common now, optical discs (CDs and DVDs) were traditionally made from polycarbonate.
- Medical and Industrial Equipment: Components that require high impact resistance and clarity, such as medical device housings and machine guards.
- Consumer Goods: Used in eyewear lenses, including safety goggles and sports eyewear, as well as in kitchenware, water bottles, and other household products; however, some manufacturers have phased out Lexan due to concerns regarding BPA.
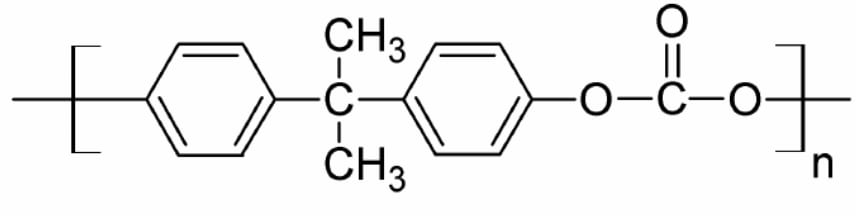
Kevlar
Kevlar is a high-strength synthetic fiber developed by DuPont in the 1960s, renowned for its exceptional strength, lightweight nature, and heat resistance. This unique combination of properties makes Kevlar invaluable in applications requiring high durability and protection, such as ballistic armor, industrial safety equipment, and various composites.
Chemical Structure:
- Aramid Fiber: Kevlar is classified as an aramid (aromatic polyamide) fiber, characterized by a molecular structure with repeating amide bonds. The benzene rings in Kevlar’s backbone contribute rigidity, while hydrogen bonds between molecular chains enhance its strength and stability.
- Crystal Alignment: Kevlar fibers are produced through a process called "liquid crystalline spinning," which aligns molecules in parallel chains. This alignment significantly boosts its tensile strength.
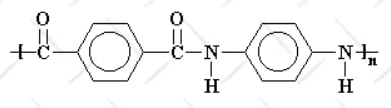
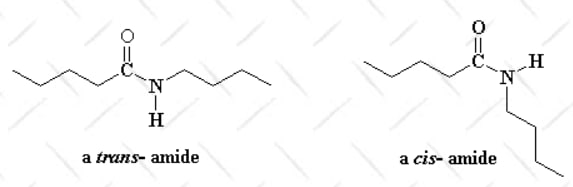
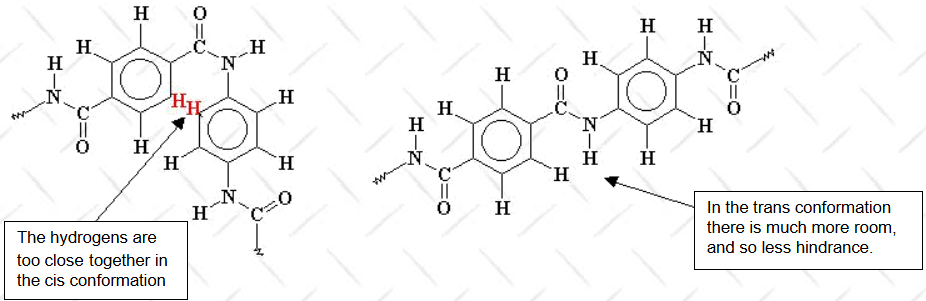
Properties:
- High Tensile Strength: Kevlar possesses remarkable strength, with a tensile strength five times greater than that of steel by weight. This makes it highly resistant to stretching and breaking under stress.
- Lightweight: Despite its strength, Kevlar is significantly lighter than steel and other protective materials.
- Heat and Flame Resistance: Kevlar can withstand temperatures up to 450°C (842°F) without degrading and is inherently flame-resistant, making it ideal for applications where fire safety is crucial.
- Abrasion Resistance: Kevlar resists cuts, wear, and abrasion, contributing to its durability, especially in protective and industrial settings.
- Low Elongation: Kevlar fibers exhibit minimal elongation or deformation under stress, allowing them to maintain their shape even under extreme conditions.
- Chemical Stability: Kevlar is resistant to many chemicals, although it can be affected by strong acids and ultraviolet (UV) light over time.
Types of Kevlar:
There are several grades of Kevlar, each designed for specific applications:
- Kevlar 29: Known for its high strength and durability, this grade is widely used in ballistic vests, ropes, cables, and protective gear.
- Kevlar 49: This high-modulus version is commonly used in fiber-reinforced composites for aerospace, marine, and automotive applications due to its strength and stiffness.
- Kevlar AP (Advanced Performance): A newer formulation with enhanced performance characteristics, offering improved protection with reduced weight; used in armor and protective equipment.
- Kevlar K129: Specifically designed for ballistic protection, this grade is utilized in armor applications, including helmets, vehicle armor, and ballistic vests.
- Kevlar XP and Kevlar AS: Newer grades optimized for flexibility and performance in ballistic protection, providing high stopping power while reducing bulk for lightweight protective gear.
Applications:
Kevlar’s exceptional properties make it valuable across various industries:
- Ballistic and Body Armor: Kevlar is best known for its use in bulletproof vests, helmets, and other personal protective equipment, as it can absorb and dissipate energy from ballistic impacts.
- Industrial Safety: Used in gloves, sleeves, and aprons to protect against cuts and abrasion in industrial settings such as manufacturing and metalworking.
- Aerospace and Automotive: Kevlar-reinforced composites are employed in aircraft, spacecraft, and high-performance vehicles due to their strength-to-weight ratio and thermal stability.
- Marine Applications: Used in hull reinforcement, ropes, and sails, where strength and resistance to stretching are critical.
- Sports Equipment: In high-impact sports such as fencing, skiing, and motorcycling, Kevlar is used to manufacture protective equipment and clothing.
- Consumer Products: Kevlar is utilized in products such as smartphone cases, high-durability outdoor gear, and even musical instrument strings due to its resilience.