Introduction
Many metals exist in nature in combined forms as oxides, carbonates, sulfides, chlorides, and silicates (except for noble metals such as Au (gold), Pt (platinum), etc.). During the extraction process, these are reduced to their metallic state from ores, requiring a considerable amount of energy.
Compounds are in a lower energy state than metals. Hence, when metals are used in various forms, they get exposed to environments such as dry gases, moisture, and liquids. Over time, the exposed metal surface begins to decay by converting into a compound.
Any process of deterioration, destruction, and consequent loss of a solid metallic material through unwanted chemical or electrochemical attacks by its environment on its surface is called corrosion. Thus, corrosion is the reverse process of the extraction of metals. Examples include:
Rusting of iron – When iron is exposed to atmospheric conditions, a layer of reddish scale and powder of is formed. Formation of a green film of basic carbonate – forms on the surface of copper when exposed to moist air containing .
Disadvantages of corrosion:
The process of corrosion is slow and occurs only on the surface of metals, but the losses incurred are enormous. Corrosion leads to the destruction of machines, equipment, building materials, and various metallic products and structures. It is estimated that global losses due to corrosion amount to approximately 2 to 2.5 billion dollars per year.
Theories of Corrosion: Corrosion can be explained by the following two theories:
- Dry or chemical corrosion.
- Wet or electrochemical corrosion.
Chemical and Electrochemical Corrosion
Dry or Chemical Corrosion
This type of corrosion mainly occurs through direct chemical reactions between the environment and the metal, such as the direct attack of atmospheric gases like , halogens, , , , or anhydrous inorganic liquids on the metal surface. There are three main types of chemical corrosion:
- Corrosion by oxygen (or) oxidation corrosion.
- Corrosion by other gases like , , and etc.
- Liquid metal corrosion.
Oxidation Corrosion
- It occurs due to the direct action of oxygen at low or high temperatures, usually in the absence of moisture.
- At high temperatures, all metals, except noble metals like Ag, Au, and Pt, are oxidized by oxygen.
- At ordinary temperatures, most metals are only slightly affected. However, alkali metals like Li, Na, K, Rb, and alkaline earth metals like Be, Ca, and Sr are rapidly oxidized.
The reactions in oxidation corrosion are as follows:
Mechanism of oxidation corrosion
Oxidation occurs first at the surface of the metal, forming a metal oxide layer that acts as a barrier to further oxidation. For oxidation to continue, either the metal must diffuse outward through the oxide layer to the surface, or oxygen must diffuse inward to the underlying metal. Although both processes occur, the outward diffusion of metal is generally faster because metal ions are much smaller and more mobile than oxide ions.
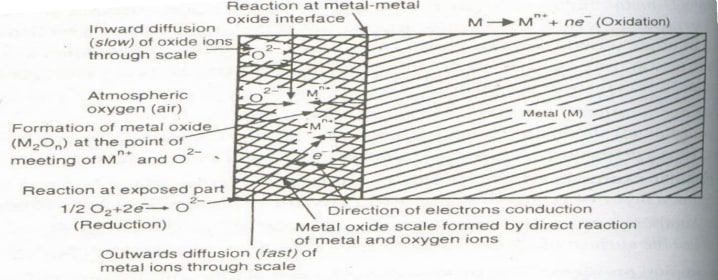
Nature of the Oxide Formed: The nature of the oxide plays an important role in the oxidation corrosion process.
Metal + oxygen metal oxide (corrosion product)
When the oxide film formed is:
-
Stable layer: - A stable layer is fine-grained and adheres tightly to the metal surface, forming an impervious barrier that protects the metal from further oxidation. E.g., Al, Sn, Pb, and Cu form stable oxide layers that prevent further corrosion.
-
Unstable Layer: - The oxide layer decomposes back into metal and oxygen, preventing oxidation corrosion.
Metal oxide metal + oxygen
Consequently oxidation corrosion is not possible in such cases.
Eg: Ag, Au and Pt do not undergo oxidation corrosion.
-
Volatile Layer: The oxide layer is volatile and evaporates as soon as it forms, leaving the underlying metal exposed for further attack. E.g., Molybdenum forms a volatile layer, leading to rapid corrosion.
-
Porous Layer: This layer contains pores and cracks, allowing atmospheric oxygen to reach the metal's surface, thus continuing the corrosion process.
E.g., Iron forms a porous FeS layer when attacked by at high temperatures.
Pilling - Bedworth rule
The oxide layer acts as a protective or non-porous barrier if the volume of the oxide is at least equal to the volume of the metal from which it is formed.
However, if the volume of the oxide layer is less than that of the metal, the oxide layer becomes porous and non-protective because it cannot prevent oxygen from reaching the fresh metal surface underneath. A lower specific volume ratio leads to a higher rate of corrosion. For example, alkali and alkaline earth metals like Li, Na, K, and Mg form oxides with volumes smaller than that of the metals.
These oxide layers are porous and non-protective, making these metals more susceptible to rapid corrosion. In contrast, metals like Al form oxides with volumes larger than that of the metal, resulting in a tightly adhering, non-porous protective layer.
Wet or Electrochemical Corrosion
This type of corrosion occurs when:
- A conducting liquid is in contact with a metal, or
- Two dissimilar metals or alloys are either immersed in or partially dipped in a solution.
The corrosion occurs due to the presence of separate anodic and cathodic areas or parts, between which current flows through the conducting solution.
- In the anodic area, an oxidation reaction occurs, meaning the anodic metal is destroyed by dissolving or forming a compound such as an oxide.
- Hence, corrosion always occurs at the anodic areas.
At the Anode:
At the Cathode:
-
In the cathodic area, a reduction reaction (gain of electrons) takes place. The metal acting as the cathode remains in its reduced form, meaning it cannot be further reduced. Therefore, cathodic reactions do not affect the cathode.
-
At the cathodic part, dissolved constituents in the conducting medium accept the electrons to form ions like , , etc.
-
The metallic ions from the anodic part and the non-metallic ions from the cathodic part diffuse toward each other through the conducting medium and form a corrosion product somewhere between the anode and cathode.
-
The electrons that are set free at the anodic part flow through the metal and are finally consumed in the cathodic region.
Key Points in Electrochemical Corrosion
- Formation of anodic and cathodic areas.
- Electrical contact between the cathodic and anodic parts to allow electron flow.
- An electrolyte that enables ions to diffuse or migrate, usually provided by moisture.
- Corrosion occurs at the anode only.
- Corrosion products form somewhere between the cathode and the anode.
Mechanism of Wet or Electrochemical Corrosion
In wet corrosion, the anodic reaction involves the dissolution of metal as corresponding metal ions, with the liberation of free electrons:
The cathodic reaction consumes electrons, either by:
- Hydrogen evolution, or
- Oxygen absorption, depending on the nature of the corrosive environment.
Theory of Electrochemical Corrosion
Electrochemical Theory of Corrosion by Hydrogen Evolution
This occurs in acidic environments. For example, in the corrosion of iron, the anodic reaction involves the dissolution of iron as ferrous ions with the liberation of electrons:
-
These electrons flow through the metal from the anode to the cathode (the acidic region), where ions are eliminated as gas:
-
The overall reaction is:
This type of corrosion displaces hydrogen ions from the acidic solution by metal ions. In hydrogen evolution corrosion, the anodic areas are large, while the cathodic areas are small. All metals above hydrogen in the electrochemical series tend to dissolve in acidic solutions, causing hydrogen evolution.
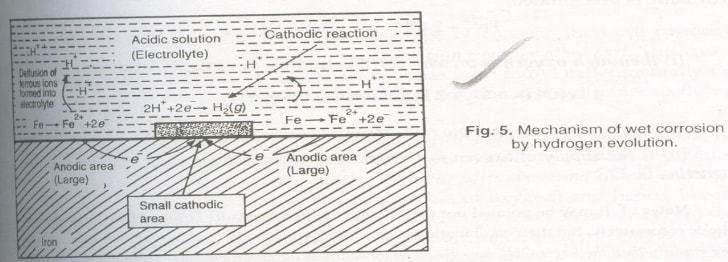
Electrochemical Theory of Corrosion by Oxygen Absorption
Rusting of iron in a neutral aqueous solution of electrolytes like NaCl in the presence of atmospheric oxygen is a common example of this type of corrosion.
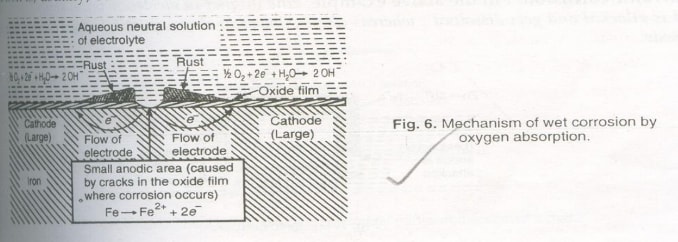
-
The surface of iron is usually coated with a thin film of iron oxide. However, if this oxide film develops cracks, anodic areas are created on the surface, while pure metal parts act as the cathode.
-
Anodic areas are very small, and the rest of the surface forms the cathode.
-
At the anodic part, iron dissolves as ions with the liberation of electrons:
-
The liberated electrons flow from the anodic to cathodic areas through the iron, where they interact with dissolved oxygen and moisture:
-
The ions and ions diffuse and form ferrous hydroxide precipitate when they meet:
-
If enough oxygen is present, is oxidized to (ferric hydroxide):
This product, known as yellow rust, corresponds to . If the oxygen supply is limited, the corrosion product may be black anhydrous magnetite .
Types of Electrochemical Corrosion: Differential Aeration Corrosion, Pitting Corrosion, Stress Corrosion
Differential Aeration Corrosion
Differential Aeration Corrosion occurs when different parts of a metal surface are exposed to varying concentrations of oxygen, leading to the formation of electrochemical cells where anodic and cathodic regions develop.
For example, a metal (say iron, Fe) partly covered with drops of salt solution undergoes differential aeration corrosion because the part of the surface covered by the salt solution becomes the less oxygenated part (the anode), while the uncovered part, exposed to air, is more oxygenated (the cathode).
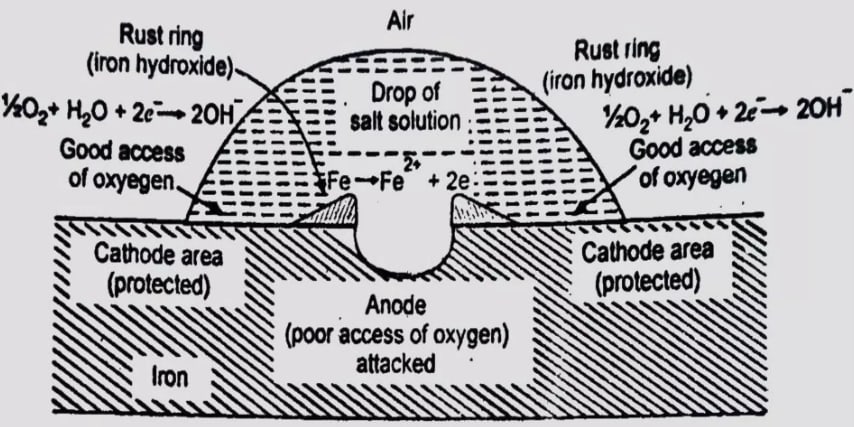
Mechanism of Differential Aeration Corrosion:
1. Formation of Anodic and Cathodic Regions
-
Anodic Region: This is the area of the metal where the oxygen concentration is low. This can occur under deposits, rust, in crevices, or areas covered by water. Here, the metal becomes more prone to oxidation, meaning it loses electrons. The general reaction at the anodic site for iron is:
-
Cathodic Region: This is the area where the metal is exposed to a higher oxygen concentration, typically in contact with air. Oxygen undergoes reduction here, and the following reaction is common:
This means that oxygen combines with water and the electrons coming from the anodic region to form hydroxide ions .
2. Electrochemical Cell Formation
The difference in oxygen concentration between the anodic and cathodic regions creates an electrochemical potential difference, leading to the formation of a galvanic cell. Electrons flow from the anodic (low-oxygen) region to the cathodic (high-oxygen) region.
3. Propagation of Corrosion
As the metal dissolves in the anodic region, it continues to oxidize (corrode). The electrons produced by this process travel to the cathodic area, where they reduce oxygen into hydroxide ions . This hydroxide can combine with metal ions in the anodic region to form rust (in the case of iron):
The ferrous hydroxide can further oxidize to form ferric hydroxide , which dehydrates to form rust .
Pitting Corrosion
Pitting corrosion is a special type of differential aeration corrosion that involves localized, accelerated attack, resulting in the formation of cavities on the metal surface. Pitting corrosion arises due to the formation of cracks, pinholes, pits, and cavities on the metal surface, which create small anodic (pit or cavity) and large cathodic areas.
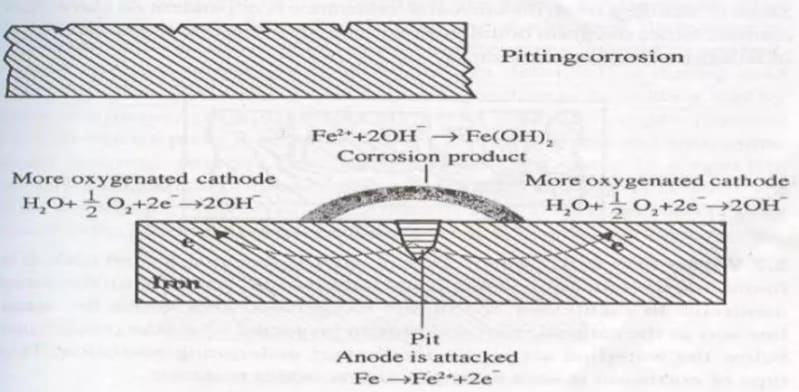
At Anode:
At Cathode:
Corrosion Product:
Stress Corrosion
Stress corrosion is a type of electrochemical corrosion that occurs when a metal is subjected to both stress and exposure to a specific electrolytic medium. The part of the metal under stress (such as sharp corners, bends, rivets, pits, joints, or crevices) acts as the anode, while the unstressed part of the metal acts as the cathode.
Pure metals are generally resistant to stress corrosion, but fabricated metal articles or metallic structures like steel alloys, brass, etc., undergo stress corrosion when exposed to specific electrolytic media and stress.
Examples:
- Brass alloy (Cu-Zn or Cu-Ni) exposed to ammonia.
- Stainless steel (containing 0.1–0.4% carbon) exposed to acid chlorides (HCl).
- Mild steel in boilers exposed to caustic alkali during the lime-soda process of water softening.
Types of Stress Corrosion:
- Season Cracking – Occurs in brass exposed to ammonia.
- Caustic Embrittlement – Occurs in mild steel in water-softening boilers exposed to caustic alkali like used in the lime-soda process.
Season Cracking
This type of corrosion typically refers to the corrosion of copper alloys, such as brass (Cu–Zn), when exposed to ammonia. When brass is exposed to ammonia solution, both copper and zinc form complexes by losing electrons, leading to the dissolution of brass at the boundaries and causing cracks for stress corrosion.
Season cracking is characterized by deep, brittle cracks that penetrate into the affected components. If the concentration of ammonia is very high, the attack becomes much more severe.
Reactions:
Caustic Embrittlement
Caustic embrittlement is a phenomenon where boiler material becomes brittle due to the accumulation of caustic substances. This type of corrosion is caused by highly alkaline water in high-pressure boilers, combined with stress. Water softened by the lime-soda process may contain , which forms from the hydrolysis of .
This corrosion typically occurs in mild steel boiler materials exposed to caustic alkali used in the lime-soda process at high temperatures and pressures. Water containing flows through small pores in stressed areas (such as bends, joints, and sharp corners) by capillary action. When the water in these areas evaporates at high temperatures, the concentration of increases compared to the unstressed parts, causing the iron to corrode by forming sodium ferroate . This leads to the embrittlement of the boiler material, particularly in stressed areas, potentially resulting in boiler failure.
Factors Affecting Rate of Corrosion – Related to Metal and Environment
Factors influencing corrosion:
- Nature of metals
- Nature of the corroding environment
Nature of Metals
-
Position in the Galvanic Series: The metal higher in the series is more active and suffers corrosion. The rate and extent of corrosion are directly proportional to the electrode potential difference between the metals.
-
Overvoltage: When a metal occupying a high position in the galvanic series (such as zinc) is placed in , it undergoes corrosion, forming a film and releasing hydrogen gas. The initial reaction rate is slow due to the high overvoltage (0.70 V) of zinc, which reduces the effective electrode potential. However, adding a few drops of copper sulfate accelerates the corrosion rate of zinc. This occurs because copper gets deposited on the zinc metal, forming minute cathodes where the hydrogen overvoltage is only 0.33 V, thus reducing the overall overvoltage and accelerating corrosion.
Zinc has a high hydrogen overvoltage, causing its corrosion rate to be slow (as in a Zn rod dipped in ). However, when is added to , copper gets deposited on the zinc rod and acts as small cathodes. Copper's hydrogen overvoltage is lower, so the rate of corrosion of zinc increases in its presence. Metals with higher overvoltage corrode more slowly, whereas those with lower overvoltage corrode more rapidly.
Example: The corrosion of a Zn rod dipped in is slow. However, when a small amount of solution is added to , copper gets deposited on the Zn rod, acting as a cathode, which increases the rate of corrosion of Zn. (The overvoltage of Zn metal is 0.73 V.)
-
Purity of Metal: Impurities in a metal generally cause heterogeneity and form minute electrochemical cells, where the anodic part gets corroded.
Example: Zn metal containing impurities such as Pb or Fe undergoes faster corrosion. The rate and extent of corrosion increase with the level of impurities.
-
Nature of the Surface Film: When metals are exposed to the atmosphere, they often become covered with a thin film of metal oxide. The ratio of the volume of metal oxide to the metal is called the specific volume ratio. The higher the specific volume ratio, the lower the rate of oxidation corrosion. For example, the specific volume ratio of Ni, Cr, and W is 1.6, 2.0, and 3.6, respectively. Consequently, the rate of oxidation corrosion is least for tungsten (W).
-
Nature of the Corrosion Product:
-
Solubility of Corrosion Products: If the corrosion product is soluble in the corroding medium, corrosion proceeds at a faster rate. If it is insoluble, corrosion is suppressed.
Example: Formation of in the case of Pb in .
-
Volatility of Corrosion Products: If the corrosion product is volatile, it evaporates as soon as it forms, leaving the underlying metal surface exposed to further attack, leading to rapid and continuous corrosion.
Example: Molybdenum (Mo) forms volatile .
-
Nature of the Corroding Environment
-
Temperature: As the temperature increases, the corrosion rate also increases because both the reaction rate and the diffusion rate of ions in the corrosion medium rise.
-
Humidity: Higher humidity in the atmosphere increases the rate and extent of corrosion since moisture acts as a medium for and behaves as an electrolyte.
Example: Atmospheric corrosion of iron is slower in dry air compared to moist air. Iron combines with and water to form ferrous hydroxide, which further reacts with in the atmosphere to form ferrous bicarbonate.
-
Effect of pH: Generally, acidic environments are more corrosive than alkaline or neutral ones. Metals can be classified based on the pH range in which they are affected or resistant. However, some metals, such as Al and Pb, are corroded in alkaline media. The corrosion rate of iron in oxygen-free water is slow until the pH drops below a certain level. Zinc corrodes rapidly in weakly acidic solutions.
Control of Corrosion
There are several methods to protect metals from corrosion:
- Barrier protection
- Sacrificial protection
- Cathodic protection
- Alloy formation
Barrier Protection
In this method, a thin barrier is developed between the surface of the metal (like iron) and the atmosphere to prevent corrosion. This can be done through:
- Uniform painting of the metal surface.
- Coating the metal surface with a thin film of non-corrosive or passive metals, such as nickel, chromium, tin, or copper.
Sacrificial Anodic Protection
In this method, the metallic structure to be protected is connected by a wire to a more anodic (active) metal, so that corrosion is concentrated on this more active metal. The more active metal corrodes slowly, while the parent structure (the metal to be protected) remains cathodic and protected.
The more active metal is called the “sacrificial anode,” and when it is completely consumed, it is replaced with a fresh one. Metals commonly used as sacrificial anodes include magnesium (Mg), zinc (Zn), aluminum (Al), and their alloys. Sacrificial anodes are used to protect buried pipelines, underground cables, marine structures, ship hulls, water tanks, and more.
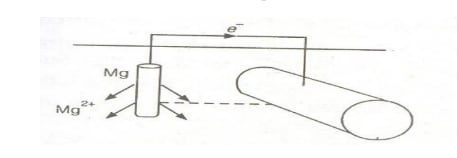
Cathodic Protection
Cathodic protection involves protecting the parent metal from corrosion by connecting it to a more active metal like magnesium (Mg), aluminum (Al), or zinc (Zn). The more electropositive (active) metal acts as the anode (supplying electrons), while the parent metal becomes the cathode (receiving electrons). The connected active metal undergoes corrosion, thereby protecting the parent metal by forcing it to act as a cathode. This method is called 'Cathodic Protection.'
Alloy Formation
Alloy formation is a method to protect metals from corrosion by combining a base metal (like iron) with one or more other metals or elements to enhance its corrosion resistance. Alloys are stronger and more durable than pure metals, and they possess properties that reduce the likelihood of corrosion.
How Alloy Formation Protects Against Corrosion
-
Formation of a Protective Layer: Some alloys form a stable, protective oxide layer on the surface that prevents further oxidation. For example, stainless steel (an alloy of iron, chromium, and nickel) forms a passive layer of chromium oxide that protects it from rusting.
-
Improved Chemical Stability: By adding elements like chromium, nickel, or aluminum, alloys become less chemically reactive and are less likely to corrode in harsh environments (e.g., marine or industrial settings).
-
Reduced Reactivity with the Environment: Alloys can be made less reactive to environmental conditions such as moisture or chemicals, thereby reducing the risk of rust and corrosion.
Examples of commonly used corrosion-resistant alloys:
- Stainless Steel (Iron + Chromium + Nickel)
- Bronze (Copper + Tin)
- Brass (Copper + Zinc)
- Aluminum Alloys (Aluminum + Magnesium or Copper)