Introduction
A fuel is any substance that undergoes chemical or nuclear changes to produce energy, which can be converted into useful work.
Typically, a fuel contains carbon and hydrogen and undergoes combustion in the presence of oxygen, releasing a large amount of energy:
Classification of Fuels
Based on their occurrence, fuels are classified into two categories: natural (primary) fuels and artificial (secondary) fuels.
- Natural/Primary fuels: These are fuels that occur naturally.
- Artificial/Secondary fuels: These are fuels synthesized from primary fuels.
Natural/Primary Fuels
- Solid Primary Fuels: Charcoal, Coke
- Liquid Primary Fuels: Petrol, Diesel, Kerosene
- Gaseous Primary Fuels: Coal gas, Water gas, Producer gas, LPG
Artificial/Secondary Fuels
- Solid Secondary Fuels: Wood, Peat, Lignite, Coal
- Liquid Secondary Fuels: Petroleum or Crude oil
- Gaseous Secondary Fuels: Natural gas
Characteristics of Good Fuel
A good fuel should have the following characteristics:
- High calorific value
- Moderate ignition temperature
- Low moisture content
- Availability in bulk at low cost
- Should not burn spontaneously
- Must burn efficiently without releasing hazardous pollutants
- Easy to handle, store, and transport
Calorific Value - Definition, HCV, LCV
The calorific value of a fuel is the amount of heat released when one unit mass or volume of the fuel undergoes complete combustion in the presence of oxygen.
A good fuel is one with a high calorific value. For example, fuels like LPG, Petrol, Kerosene, and Biogas are considered to have high to moderate calorific values, with LPG having the highest.
-
High or Gross Calorific Value (HCV or GCV):
It is defined as the amount of heat released when one unit mass or volume of fuel is completely burned, and the combustion products are cooled to room temperature (C or F). -
Low or Net Calorific Value (LCV or NCV):
It is defined as the amount of heat released when one unit mass or volume of fuel is completely burned, and the combustion products are allowed to escape. Thus, LCV is lower than HCV.Since one part by mass of hydrogen produces nine parts of water, the formula becomes:
Where H is the percentage of hydrogen in the fuel.
Determination of Calorific Value of Solid and Liquid Fuels Using a Bomb Calorimeter
A bomb calorimeter is used to experimentally determine the calorific value of solid and liquid fuels. It consists of a cylindrical bomb made of stainless steel where combustion takes place. The bomb is placed inside a copper calorimeter, surrounded by air and water jackets to prevent heat loss by radiation. The calorimeter setup includes a stirrer and a Beckmann thermometer (which can measure temperature differences as small as C).
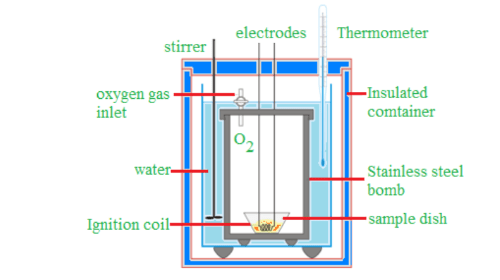
Working:
- A known amount of the fuel is placed in a nickel or stainless steel crucible inside the bomb.
- A magnesium wire touches the fuel, which is connected to electrodes.
- The bomb is filled with oxygen at 25 atm pressure and placed in a copper calorimeter containing a known amount of water.
- The initial temperature of the water, , is recorded.
- The circuit is completed, igniting the fuel sample, which liberates heat.
- The stirrer ensures a uniform temperature in the water, and the final temperature, , is recorded.
Calculation:
- Mass of fuel (solid or liquid) = g
- Mass of water taken = g
- Water equivalent of calorimeter = g
- Initial temperature of water in calorimeter = K
- Final temperature of water in calorimeter = K
To determine LCV, apply the formula:
Where H is the percentage of hydrogen in the fuel.
Corrections in Bomb Calorimeter Calculation
When calculating the HCV or GCV, you must also account for various corrections:
Where:
- = cooling corrections
- = correction for sulphuric acid ()
- = correction for nitric acid ()
- = correction for fuse wire
- = correction for cotton thread
Ultimate Analysis of Coal and Numerical Problems
The quality of coal is analyzed by proximate and ultimate analysis.
-
Proximate Analysis This involves determining moisture, volatile matter, ash, and fixed carbon content in the coal.
-
Moisture: A finely powdered coal sample is dried in an oven at to C for 1 hour. The weight loss is used to calculate the moisture content. Lesser the amount of moisture content, better the quality of fuel.
-
Volatile Matter: The moisture-free coal sample is heated in a muffle furnace at C for 7 minutes. The weight loss gives the volatile matter content. Low quantity of volatile matter, better the quality of a coal.
-
Ash: The coal sample is heated without a lid in a muffle furnace at C until a constant weight is obtained. The ash content is then determined. Ash is non-combustible substance which reduces the calorific value of a coal. Therefore, low quantity of ash contents, better the quality of a coal.
-
Fixed Carbon: This is calculated by subtracting the sum of moisture, volatile matter, and ash from 100. Greater the calorific value, higher the % of fixed carbon.
-
-
Ultimate Analysis
Ultimate analysis involves the measurement of C, H, N, S, and O.
-
Carbon and Hydrogen: In a combustion apparatus, about 1–2 grams of a coal sample are burned in a current of oxygen to convert C and H into and , respectively.
The gaseous products and are absorbed in KOH and tubes of known weights, respectively.
The increase in the weights of these (KOH and ) is then determined.Calculation:
-
Nitrogen: In a Kjeldahl’s flask, an accurately weighed powdered coal sample is heated with concentrated and as a catalyst.
The solution becomes clear when all the nitrogen is converted into ammonium sulfate. It is then treated with an excess of NaOH, which converts ammonium sulfate into ammonia.
The liberated ammonia is distilled and absorbed in a known volume of standard (N/10) solution.
From the volume of used by the liberated ammonia, the percentage of nitrogen in the coal is calculated as follows:The volume of unused is then determined by titrating against a standard NaOH solution (N/10).
Calculation:
The amount of required to neutralize the ammonia evolved from coal is calculated as follows:
Thus,
- = Volume of standard (N/10) solution
- = Volume of standard NaOH (N/10) solution
-
Sulphur: A known amount of the coal sample is burned in a bomb calorimeter in the presence of oxygen.
Sulphur in the coal is converted into and . The ash obtained from the bomb calorimeter is extracted with dilute HCl.
The washings (acid extracts) are treated with barium chloride solution, and the sulfates precipitate as barium sulfate.
This precipitate is filtered, washed, dried, and heated to obtain a constant weight.Calculation:
Thus,
Ash: The percentage of ash is calculated using the method given in proximate analysis.
Oxygen: It is calculated by subtracting the sum of the total percentages of carbon, hydrogen, nitrogen, Sulphur, and ash from 100.
Calculation:
-
Petroleum Cracking - Fluidized Bed Catalytic Cracking
Petroleum cracking is a chemical process in which large hydrocarbon molecules (usually from petroleum) are broken down into smaller, more useful molecules, such as gasoline, diesel, and other valuable products.
One of the most common methods of cracking is Fluidized Bed Catalytic Cracking (FCC).
Fluidized Bed Catalytic Cracking (FCC)
Fluidized Bed Catalytic Cracking (FCC) is a key process in the petroleum refining industry.
It is used to convert heavy fractions of petroleum crude oils into lighter, more valuable products like gasoline, diesel, and olefins (e.g., propylene and ethylene).
FCC involves breaking long-chain hydrocarbons (from heavy oils) into shorter-chain hydrocarbons using a catalyst in a "fluidized" state. The fluidized state is achieved by suspending solid catalyst particles in a stream of vaporized hydrocarbons.
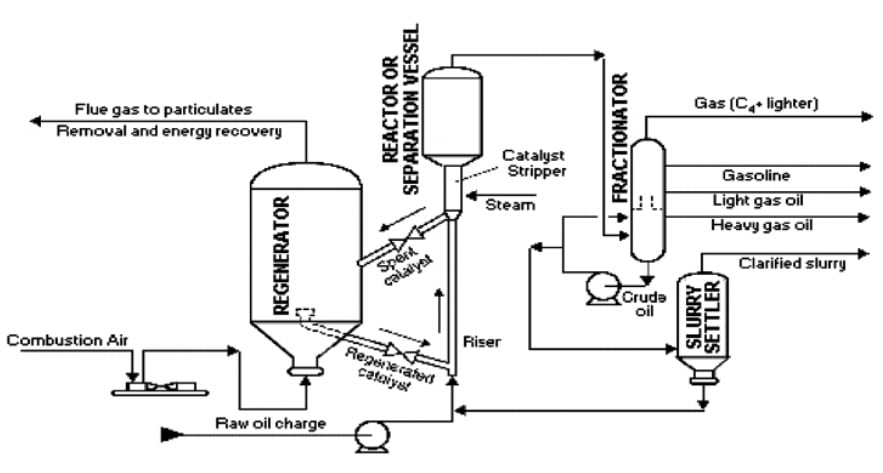
FCC Process:
-
Pre-heating and Vaporization: The heavy oil feed is preheated and vaporized before entering the reactor.
-
Cracking in the Reactor: The vaporized hydrocarbons mix with the fluidized catalyst in the reactor.
At temperatures between 450°C and 550°C, the heavy hydrocarbons break down into smaller, lighter molecules.
The reaction produces a range of products, including:- Gasoline (high-octane, desirable for fuel)
- Diesel
- Light gases (like ethylene and propylene)
- Coke (solid carbon byproduct)
-
Separation: The cracked hydrocarbons are separated from the catalyst in cyclones. The hydrocarbons move to a distillation unit where they are separated into different products (e.g., gasoline, diesel, LPG).
-
Regeneration: The coked catalyst, after losing its activity, is sent to the regenerator. In the regenerator, air is introduced, and the coke is burned off the catalyst at high temperatures (around 600°C). This regenerates the catalyst, and the heat generated is reused in the process.
-
Recycling: The regenerated catalyst is then returned to the reactor, and the cycle continues.
Advantages of FCC
- Improves Yield of Light Products: FCC significantly increases the yield of lighter products, like gasoline and propylene, from heavy fractions of crude oil.
- Catalyst Regeneration: Continuous regeneration of the catalyst ensures efficient cracking over long periods, making FCC a highly productive process.
- Enhanced Product Quality: FCC produces high-octane gasoline, which is highly desirable for modern engines, and a variety of valuable petrochemicals.
- Flexibility: The process can handle a wide variety of feedstocks, from heavy oils to residual fractions.
Challenges in FCC
- Coking: The formation of coke on the catalyst reduces its activity and must be continually burned off.
- Environmental Concerns: The burning of coke generates and other emissions, which are environmental concerns.
- Catalyst Poisoning: Impurities in the feedstock, such as sulfur and heavy metals, can "poison" the catalyst and reduce its effectiveness.
Reformation of Petrol
Crude oil obtained from the earth is not fit for marketing. It contains many soluble and insoluble impurities that must be removed. Previously, the purification of crude oil was done by simple fractional distillation. Further treatment of the products is carried out through refining. The process by which petroleum is made free of impurities, followed by the separation of petroleum into different fractions with different boiling points, and their further treatment to impart specific properties, can be called the refining of petroleum.
The stages of the refining process are:
- Removal of solid impurities.
- Removal of water.
- Removal of harmful impurities.
- Fractional distillation.
-
Removal of solid impurities
Crude oil is a mixture of solid, liquid, and gaseous substances. It is allowed to stand undisturbed for some time, until the heavy solid particles settle down and the gases evaporate. The supernatant liquid is then centrifuged, where the solids are removed.
-
Removal of water by Cottrell's process
The crude oil obtained from the earth's crust is in the form of a stable emulsion of oil and brine. This mixture, when passed between two highly charged electrodes, causes the emulsion films to break, and the colloidal water droplets coalesce into larger drops, which then separate from the oil.
-
Removal of harmful impurities
To remove sulfur compounds in crude oil, it is treated with copper oxide. The sulfur compounds are converted into insoluble copper sulfide, which can be removed by filtration. Substances like NaCl and , if present, can corrode refining equipment and result in scale formation. These can be removed by techniques like electric desalting and dehydration.
-
Fractional distillation
Crude oil is fractionally distilled in a fractionating still, a tower-like structure with bubble trays inside. The crude oil enters through the bottom of the still via an inlet. It passes through a pre-heater or is heated with steam inside the still to a temperature of about 400°C. As we move up the fractionating still, the temperature decreases. Several side pipes are fitted at different heights of the column or still to collect the fractions. As petroleum enters the still, it vaporizes, and the vapors rise through the bubble tower.
The bubble tower consists of several horizontal trays, each equipped with small chimneys through which the vapors rise. The chimneys are covered with loose caps so that the vapors bubble through and condense, dropping back into the trays. As the vapors move up, they become cooler, and fractional condensation of the crude oil occurs at different levels in the bubble tower. The vapors of the liquids with the highest boiling points condense first and exit, while those with the lowest boiling points condense last, along with the uncondensed gases.
Quality of Liquid Fuels - Cetane and Octane Number
The quality of liquid fuels is a crucial factor in determining how efficiently they burn in engines. Two key metrics for measuring the quality of liquid fuels, specifically for diesel and gasoline, are the Cetane number and the Octane number, respectively.
Octane Number
The Octane number is defined as the percentage of isooctane present in a standard mixture of isooctane and n-heptane, which knocks at the same compression ratio as the petrol being tested. Isooctane, a branched-chain hydrocarbon, has the least knocking tendency, and its Octane number is arbitrarily fixed at 100. n-Heptane, a straight-chain hydrocarbon, has the highest tendency to knock, and its Octane number is set at zero. An Octane number of 80 means the petrol contains 80% by volume of isooctane and 20% by volume of n-heptane.
The Octane number is determined by comparing the fuel to two reference hydrocarbons:
- Iso-octane : A highly knock-resistant hydrocarbon, with an Octane number of 100.
- n-Heptane : A highly knock-prone hydrocarbon, with an Octane number of 0.
How the Octane Number Works:
- Gasoline engines use spark ignition to ignite the air-fuel mixture.
- A fuel with a higher Octane number is more resistant to knocking and can withstand higher compression before igniting.
- Fuels with a low Octane number are more prone to pre-ignition (knocking), which can damage the engine over time.
Cetane Number
The Cetane number is defined as the percentage of cetane present in a standard mixture of cetane and alpha-methylnaphthalene, which knocks at the same compression ratio as the diesel fuel being tested.
The Cetane number is measured by comparing the fuel to two reference hydrocarbons:
- n-Cetane : A high Cetane hydrocarbon (Cetane number = 100), meaning it ignites easily.
- Alpha-methylnaphthalene: This hydrocarbon has a lower Cetane number and does not ignite as easily.
How the Cetane Number Works:
- Diesel engines rely on compression ignition, where the fuel is injected into highly compressed air, causing it to ignite from the heat of the air.
- A fuel with a higher Cetane number will ignite more readily, leading to a shorter ignition delay and smoother combustion.
- Fuels with a low Cetane number may cause engine knock, noise, or misfiring due to delayed ignition, which can lead to inefficiency and wear on engine components.
Power Alcohol - Manufacture
A mixture of ethyl alcohol and gasoline, used as a fuel in internal combustion engines, is known as power alcohol or gasohol. Absolute alcohol is mixed with compounds like ether and benzene, and one volume of this mixture is combined with four volumes of petrol to be used as fuel.
Manufacture of Power Alcohol
The production of power alcohol primarily involves the manufacture of ethanol, which is then mixed with gasoline. The ethanol used in power alcohol is obtained from the fermentation of biomass (such as sugarcane, corn, or other agricultural products) or from the synthesis of petrochemicals.
-
Manufacture of Ethyl Alcohol:
Ethyl alcohol can be synthesized by the fermentation of carbohydrates (sugar material).
Fermentation of molasses, which is the residue left after the crystallization of sugar, with yeast generates alcohol.
This fermentation yields only about 20% alcohol.The concentration of alcohol can be increased to 97.6% by fractional distillation, yielding rectified spirit.
The concentration of alcohol cannot be increased by distillation beyond 97.6%, as it forms a constant boiling mixture with water.
This constant boiling mixture has a lower boiling point than alcohol. -
Conversion of Ethyl Alcohol into Power Alcohol:
For use in internal combustion (IC) engines, 100% alcohol (absolute alcohol) is required by removing the last traces of water from rectified spirit.
This can be done using the following two methods:- Alcohol containing traces of water is distilled with benzene. As benzene passes over with a portion of alcohol and water, it leaves behind absolute (power) alcohol.
- Alcohol is distilled in the presence of a dehydrating agent, which binds the water.
Properties
- Power alcohol has a lower calorific value (7000 kcal/kg).
- It has a high octane number (90).
- It possesses good anti-knocking properties.
- It generates 10% more power than gasoline of the same quantity.
- Its compression ratio is higher.
Advantages
- The power output is good.
- It has better anti-knock properties.
- Ethanol is biodegradable, making it an environmentally friendly fuel.
- The use of ethanol in alcohol increases the oxygen content of fuels and promotes more complete combustion of hydrocarbons in gasoline.
- It reduces carbon monoxide emissions.
Disadvantages
- As the calorific value of power alcohol (7000 cal/g) is lower than that of petrol (11,500 cal/g), a specially designed engine is required.
- Output power is reduced by up to 35%.
- Due to its high surface tension, the atomization of power alcohol is difficult, causing starting problems.
- It may undergo oxidation to produce acetic acid, which can corrode engine parts.
Concept of Hydrogen as Fuel - Types
Hydrogen (H₂) can be used as a fuel by either combusting it in internal combustion engines (ICE) or through electrochemical reactions in fuel cells.
When hydrogen is burned or used in a fuel cell, it reacts with oxygen (O₂), and the primary by-product is water (H₂O), along with the release of energy.
Hydrogen as a Clean Fuel
-
Combustion: In a combustion engine, hydrogen is burned with oxygen in a manner similar to gasoline or natural gas. The reaction is:
The only emission is water vapor, making it a zero-emission fuel from a pollution perspective.
However, some nitrogen oxides (NOₓ) might be produced under high combustion temperatures. -
Fuel Cells: Hydrogen is primarily used in fuel cells, where it generates electricity through an electrochemical process rather than combustion.
The most common type is the Proton Exchange Membrane (PEM) fuel cell, where hydrogen reacts with oxygen to generate electricity, water, and heat.The fuel cell is highly efficient, and no harmful emissions are produced apart from water.
Types of Hydrogen Fuels
Hydrogen fuel can be classified based on its production source into three types:
-
Grey Hydrogen:
-
Produced from natural gas through a process called steam methane reforming (SMR).
This is the most common and cost-effective method currently used, but it releases large amounts of carbon dioxide (CO₂), contributing to greenhouse gas emissions. -
Environmental Impact: High due to CO₂ emissions.
-
-
Blue Hydrogen:
-
Produced from natural gas (through SMR) but with carbon capture and storage (CCS) technology, which traps the carbon dioxide and prevents it from entering the atmosphere.
-
Environmental Impact: Much lower than grey hydrogen as CO₂ is captured and stored.
-
-
Green Hydrogen:
-
Produced by the electrolysis of water, where electricity (from renewable sources like solar or wind) is used to split water into hydrogen and oxygen.
This method produces hydrogen without any carbon emissions, making it the most environmentally friendly. -
Environmental Impact: Zero emissions if renewable energy sources are used.
-
Advantages of Hydrogen as a Fuel
- Hydrogen is a clean fuel, with water as the only emission, especially when produced using renewable energy.
- Hydrogen has a high energy density (120-142 MJ/kg), which is almost three times that of gasoline (44-46 MJ/kg).
- Hydrogen can be used for transportation, power generation, and heating applications.
- Hydrogen can be produced locally from various sources, reducing dependence on fossil fuels.
- Hydrogen can be stored for long periods, making it a good option for balancing energy supply and demand.
Challenges of Hydrogen as a Fuel
- The cost of producing green hydrogen is still high due to the energy required for electrolysis and the cost of renewable energy.
- Hydrogen is difficult to store and transport because it is the lightest element, requiring high-pressure storage systems or liquefaction at very low temperatures.
- The current infrastructure for hydrogen fueling (like hydrogen refueling stations) is limited, especially for widespread adoption in transportation.
- Hydrogen is highly flammable and needs careful handling to avoid leaks and explosions.
Synthesis by Water Electrolysis and Natural Gas Reforming
Hydrogen can be synthesized by two main processes: water electrolysis and natural gas reforming.
Both methods are widely used but have different implications in terms of environmental impact, efficiency, and cost.
Synthesis of Hydrogen by Water Electrolysis
Water electrolysis is a process in which water (H₂O) is split into hydrogen (H₂) and oxygen (O₂) using an electric current.
This method can produce green hydrogen when the electricity used comes from renewable sources such as solar or wind energy.
Process of Electrolysis:
-
Electrolysis Reaction:
-
Electrolyzer: An electrolyzer passes an electric current through water, causing it to dissociate into hydrogen and oxygen.
The electrolyzer consists of two electrodes (an anode and a cathode) and an electrolyte that conducts ions.Cathode: Water molecules gain electrons and are reduced to hydrogen gas and hydroxide ions (OH⁻).
Anode: Water molecules are oxidized to form oxygen gas, protons (H⁺), and release electrons.
Types of Electrolysis
- Alkaline Electrolysis: Uses a liquid alkaline electrolyte (e.g., potassium hydroxide) to conduct ions. It is a mature and well-understood technology but has lower efficiency.
- Proton Exchange Membrane (PEM) Electrolysis: Uses a solid polymer membrane as the electrolyte. It is more efficient and compact but has higher costs.
- Solid Oxide Electrolysis (SOE): Uses a solid ceramic electrolyte and operates at high temperatures, improving efficiency but requiring heat input.
Advantages of Water Electrolysis
- Zero carbon emissions if renewable electricity is used, making it environmentally friendly.
- High purity hydrogen is produced.
- Can store excess renewable energy in the form of hydrogen, which can later be converted back to electricity.
Challenges
- Electrolysis requires a significant amount of electricity, making it costly if not sourced from cheap, renewable energy.
- Electrolyzers are still relatively expensive to build and maintain compared to traditional methods like natural gas reforming.
Synthesis of Hydrogen by Natural Gas Reforming
Natural gas reforming, also known as steam methane reforming (SMR), is the most common and cost-effective method for hydrogen production today.
This method involves reacting natural gas (mostly methane, CH₄) with steam to produce hydrogen, carbon monoxide, and carbon dioxide.
It produces grey hydrogen when the carbon emissions are not captured and blue hydrogen when coupled with carbon capture and storage (CCS) technologies.
Process of Steam Methane Reforming (SMR):
-
Reforming Reaction: In the first step, methane (CH₄) reacts with steam (H₂O) in the presence of a nickel-based catalyst at high temperatures (700–1000°C) to produce hydrogen (H₂), carbon monoxide (CO), and some carbon dioxide (CO₂).
-
Water-Gas Shift Reaction: The carbon monoxide produced in the first reaction reacts with additional steam to produce more hydrogen and carbon dioxide.
The overall reaction is:
Carbon Capture (for Blue Hydrogen):
In blue hydrogen production, the carbon dioxide (CO₂) produced during the SMR process is captured and stored underground or used in other industrial processes to prevent it from being released into the atmosphere.
Advantages of Natural Gas Reforming
- SMR is the most economically viable method for large-scale hydrogen production today, especially in regions with abundant natural gas.
- It has been in use for decades, and the infrastructure for natural gas and SMR plants is already well-developed.
Challenges
- SMR produces significant amounts of CO₂, contributing to climate change. Even with carbon capture, not all emissions can be prevented.
- Hydrogen production through SMR is dependent on fossil fuels, which are finite and contribute to global warming.
Comparison of Water Electrolysis and Natural Gas Reforming
Aspect | Water Electrolysis | Natural Gas Reforming (SMR) |
---|---|---|
Hydrogen Type | Green hydrogen (if renewable energy is used) | Grey hydrogen (without CCS), Blue hydrogen (with CCS) |
Feedstock | Water | Natural gas (methane) |
By-products | Oxygen (O₂), no harmful emissions | Carbon dioxide (CO₂), carbon monoxide (CO) |
Energy Efficiency | ~60-70% (high energy demand) | ~70-85% |
Environmental Impact | Zero emissions if renewable electricity is used | High CO₂ emissions unless CCS is implemented |
Cost | Higher (due to electricity costs and electrolyzer setup) | Lower (natural gas is cheaper) |
Technological Maturity | Emerging technology | Mature, widely used |